Micro EDM is a precision machining process that utilizes electrical discharges to remove small amounts of material from a workpiece. It differs from traditional EDM in that it is used to create smaller and more intricate shapes with higher accuracy and precision. Micro EDM is widely used in a variety of industries, including aerospace, medical, and electronics. Read More…
XACT Wire EDM Corp. is one of the largest and most experienced Wire EDM Companies in the country. Our Wire EDM manufacturing capabilities include a large number of high-end machines with two locations offering advanced CMM and video inspection. We work with a wide variety of customers in the medical, defense, aerospace, automation, robotics industries as well as many companies in the metal...

Twin City is ISO 9001:2000 certified for all simple & complex EDM services, in addition to many other services & their forte is producing difficult, complex parts through their state-of-the-art equipment & highly skilled staff. TC will perform the nearly impossible & is known to give both 100% in quality & service. Our flexibility & versatility provide customers with affordable convenience.
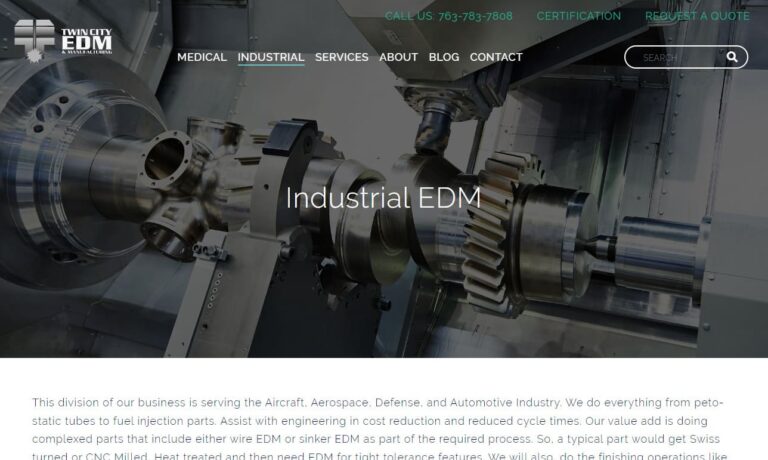
At B&B Precision Wire EDM, Inc., we take pride in delivering cutting-edge EDM solutions that redefine precision and efficiency. With a relentless commitment to excellence, our team crafts a diverse range of EDM products that cater to the evolving needs of industries worldwide.

AMI Machining, Inc. takes pride in our unwavering commitment to excellence in the realm of Electrical Discharge Machining (EDM). We have consistently been at the forefront of innovation and precision in the manufacturing industry.
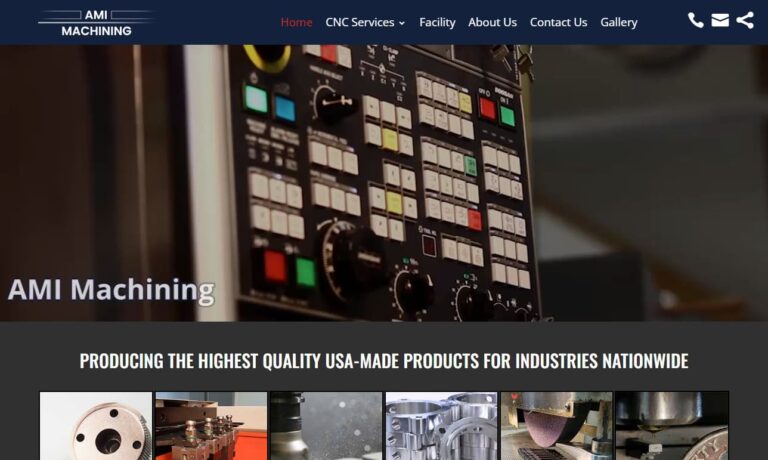
Conventional electronic discharge machining and wire EDM machining take place here at Aerospace Techniques. We machine items that are "out of the norm" due to complexity, material or shape. Since 1965, our machining services have been used for aerospace, aircraft engine and medical customers. Contact Aerospace Techniques today to get a quote for your next project!
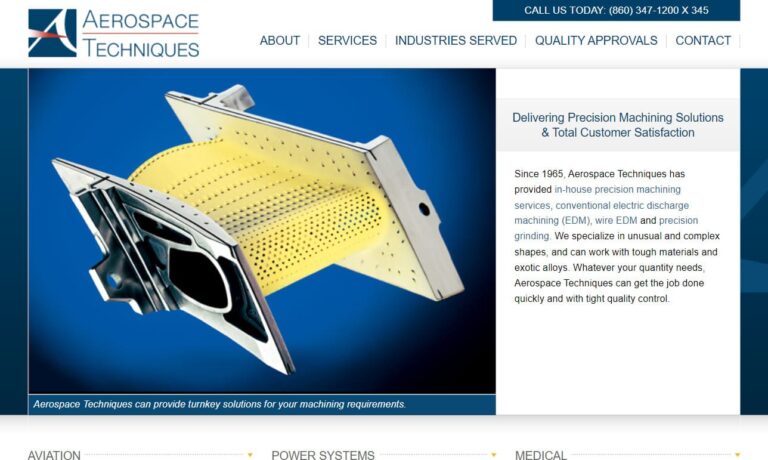
More Micro EDM Companies
How Micro EDM Is Performed
Micro EDM is performed using a specialized machine that uses electrical discharges to remove material from the workpiece. The process involves creating a spark between an electrode and the workpiece, which erodes the material in the desired shape. The electrode and the workpiece are submerged in a dielectric fluid, which helps to cool the material and remove debris.
Equipment Used in Micro EDM
Micro EDM machines use a variety of specialized equipment, including micro electrodes, micro machining tools, and specialized software. The micro electrodes are typically made from tungsten, copper, or graphite and are used to create the desired shape in the workpiece. Micro machining tools are used to control the movement of the electrode and ensure precision in the machining process.
Considerations Regarding Micro EDM
EDM, in general, has some considerations to account for, including the potential for surface cracking, surface roughness, and the production of recast layers. These issues can also occur in micro EDM, as the process is essentially the same as traditional EDM but on a smaller scale. Surface cracking, surface roughness, and the production of recast layers can also occur in micro EDM, especially if the process is not optimized for the specific workpiece material or geometry. Micro EDM, specifically, can also be affected by factors such as electrode wear, material deformation, and thermal damage.
Benefits of Micro EDM
EDM offers a range of benefits, including the ability to create complex shapes with high accuracy and precision. EDM is also a non-contact machining process, which means that there is no physical contact between the electrode and the workpiece, reducing the risk of damage to the material. These benefits are shared by micro EDM.
Additionally, there are several other benefits of micro EDM over traditional EDM. One key advantage of micro EDM is that it can be used to machine parts with high aspect ratios, which is the ratio of the depth of a hole or groove to its width. Micro EDM can create deep, narrow channels or holes that would be difficult or impossible to produce with other machining processes. This is especially important in industries such as medical and aerospace, where small and complex parts with high aspect ratios are common. Another advantage of micro EDM is that it can be used to create precise and uniform microstructures on the surface of a workpiece. This is useful in applications where a specific texture or pattern is needed for functional or aesthetic reasons. For example, micro EDM can be used to create microchannels on the surface of a medical implant to encourage bone growth, or to create precise patterns on the surface of a watch face. Finally, micro EDM can also be used to machine parts with high hardness and wear resistance, such as tungsten carbide and diamond. These materials are often used in cutting tools and other high-performance applications, and traditional machining processes can struggle to work with them. Micro EDM, however, is able to create precise and complex shapes in these materials, making it a valuable tool in industries where these materials are common.
Applications of Micro EDM
Micro EDM has a wide range of applications in industries such as medical, aerospace, and electronics. In the medical industry, micro EDM can be used to create small and precise medical implants, such as bone screws, dental implants, and artificial joints. Micro EDM can also be used to create microfluidic channels and sensors for diagnostic devices and drug delivery systems. In the aerospace industry, meanwhile, micro EDM can be used to create small and complex parts for aircraft engines, such as fuel injectors and turbine blades. Additionally, the electronics industry uses micro EDM to create micro-molds for microchip packaging and to create microelectrodes for electronic devices.
Another application of micro EDM is in the creation of micro-molds and micro-dies for micro injection molding and micro stamping processes. Micro EDM can be used to create complex and precise shapes in the molds and dies, which are then used to create small and intricate parts for a range of applications. This is particularly useful in the production of small mechanical and electronic components, such as gears, springs, and connectors. Micro EDM can also be used in the creation of micro-electromechanical systems (MEMS). MEMS are devices that combine electronic and mechanical components on a microscopic scale and are used in a range of applications, including sensors, actuators, and microfluidic devices. Micro EDM can be used to create the microstructures and micro-components needed for these devices, such as microchannels, micro-valves, and micro-gears. Finally, micro EDM can be used in the creation of micro-optical components, such as micro-lenses and micro-mirrors. These components are used in a range of applications, including telecommunications, medical imaging, and scientific research. Micro EDM can create the precise shapes and surface finishes needed for these components, making it a valuable tool in the production of high-quality optical components.
Choosing the Proper Micro EDM Machining Company
To ensure you have the most positive outcome when selecting a micro EDM machining business, it is important to compare several micro EDM machining companies using our directory of micro EDM machining companies. Each micro EDM machining company has a business profile page highlighting their areas of experience and capabilities, along with a contact form to directly communicate with them for more information or request a quote. Review each micro EDM machining company website using our proprietary website previewer to learn what each company specializes in. Then, use our simple RFQ form to contact multiple micro EDM businesses with the same form.